一、结构特点
炉体设计
炉体通常采用耐高温材料(如高铝砖、碳化硅等)制成,内部设计有加热区、保温区和冷却区,确保焙烧过程中温度均匀分布。部分炉体采用模块化设计,便于维护和更换部件。
加热系统
加热方式包括燃气燃烧、电加热或燃油加热,部分设备采用热风循环系统,通过风机将热风均匀输送至炉内,提高热效率。
控制系统
配备先进的自动化控制系统,可实时监测和调节炉内温度、气氛(如氧气含量)和压力,确保焙烧过程稳定可控。部分设备支持远程监控和故障诊断功能。
出料系统
出料口设计有冷却装置,防止氧化铝球在高温下氧化或结块。出料方式包括螺旋输送、振动给料等,确保产品连续稳定输出。
二、工作原理
预热阶段
氢氧化铝原料通过进料装置进入炉体,在低温区(约200-300°C)预热,去除表面水分。
焙烧阶段
原料进入高温区(900-1200°C),发生脱水反应和晶型转变,生成γ-Al₂O₃或α-Al₂O₃。此阶段需严格控制温度和气氛,避免产品烧结或氧化。
冷却阶段
焙烧后的氧化铝球进入冷却区,通过自然冷却或强制风冷迅速降温,防止晶型转变或性能劣化。
三、技术优势
高效节能
采用热风循环和余热回收技术,降低能耗;自动化控制系统优化加热曲线,减少能源浪费。
产品质量稳定
精确的温度和气氛控制确保氧化铝球的晶型、比表面积和活性等指标符合标准,满足电解铝、催化剂等行业需求。
环保性能
部分设备配备脱硝、脱硫装置,减少氮氧化物和硫氧化物的排放;低噪音设计降低对环境的影响。
操作便捷
自动化程度高,减少人工干预;模块化设计便于维护和升级。
四、应用场景
电解铝行业
作为电解铝生产的原料,高纯度氧化铝球的需求量巨大,焙烧炉需具备大规模连续生产能力。
催化剂载体
用于制备催化剂载体(如分子筛、活性氧化铝),要求产品具有高比表面积和孔隙率。
陶瓷与耐火材料
生产高性能陶瓷和耐火材料时,需使用特定晶型的氧化铝球,焙烧炉需满足定制化工艺需求。
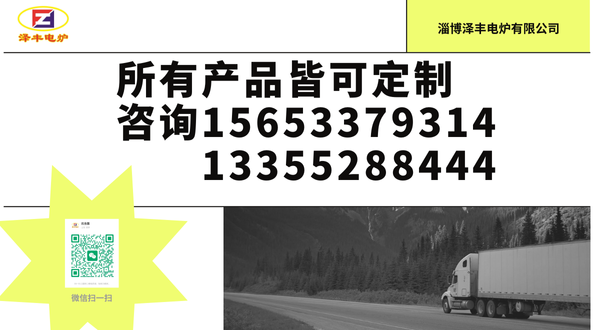